Sustainable and future-proof temperature control
Natural hydrocarbons as a climate-friendly refrigerant
The decision for a refrigerant in a temperature control unit is often complex and a compromise between various factors. Depending on the application, chemical, thermodynamic, fluid dynamic and physical properties must be taken into account. In addition, the environmental impact is becoming increasingly relevant - and not just since the EU F-Gases Regulation came into force. Natural refrigerants offer excellent energy efficiency combined with known environmental compatibility. Peter Huber Kältemaschinenbau AG has been using hydrocarbons in its refrigeration machines for many years, making it one of the pioneers of environmentally compatible temperature control technology.
In the past, the refrigeration industry mainly used HFC refrigerants such as R134a, R507A and R404A. These refrigerants are non-flammable and have good thermodynamic properties in the low-temperature range down to about -50°C. For these synthetically produced fluorinated gases (F-gases), the environmental compatibility is determined on the basis of the ozone depletion potential ODP (Ozone Depletion Potential) and the global warming potential GWP (Global Warming Potential).
While the Montreal Protocol of 1987 restricted the gases with ozone depletion potential, the current EU F-Gases Regulation (EU NR. 517/2014) refers to the gases with global warming potential. The F-Gases Regulation has a target to reduce the maximum amount of refrigerants placed on the market annually to 21% by 2030. To achieve this target, the maximum quantity has been gradually reduced since 2016 in a phase down process (→ Fig. 1). Parallel to the phase down, additional GWP ceilings are set for various applications. Temperature control units are classified as stationary refrigeration systems and may have a maximum GWP of 2500 from 01.01.2020. Devices with an operating temperature below -50 °C are excluded from this.
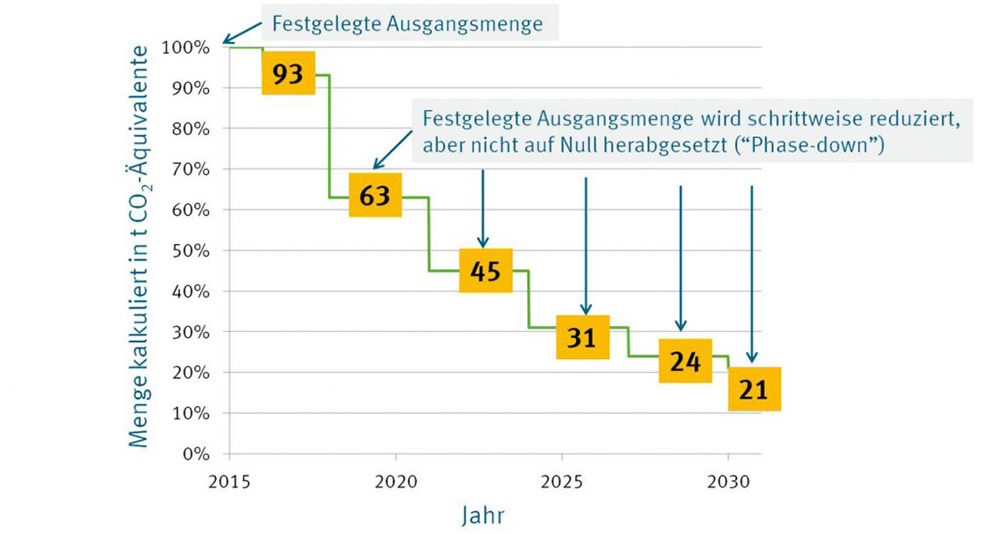
As early as the early 1970s, company founder Peter Huber gained his first experience with natural refrigerants. In the following years, numerous series devices with propane R290 and propene R1270 were developed and launched internationally. These refrigerants have no ozone depletion potential and only a low global warming potential (GWP = 2-3). However, despite all the pioneering work, some users are still skeptical about natural refrigerants. The main reason for this is safety concerns due to flammability. The fact that these concerns are unfounded is proven by Huber's laboratory units, which have been sold thousands of times and are accident-free. The compact circulators (Unichiller, Minichiller, → Fig. 2), process thermostats (Petite Fleur, Tango) and refrigeration thermostats (KISS, Ministat, etc.) have been equipped with propane R290 or propene R1270 as standard for many years. The refrigerant charge in these models is less than 150 g, so no safety measures are usually required. Larger temperature control systems, such as the Unistat 610 with a charge of 2.2 kg, are also available with natural refrigerant on request. In this case, however, measures are required on the part of the operator to ensure compliance with safety regulations. Depending on the installation site and intended use, suitable ventilation must be ensured and a gas warning sensor installed, among other things.
There is no real alternative to natural refrigerants. There are currently no known non-flammable and non-toxic synthetic refrigerants with comparable physical properties. This also applies to the new group of HFO refrigerants (hydrofluoroolefins) such as R1234yf. Although these refrigerants have a low global warming potential, they are also flammable. Consequently, the classification in the safety data sheet does not make any difference, i.e. the risk assessment must be carried out for flammable synthetic refrigerants to the same extent as for flammable natural refrigerants. Overall, it should be noted that the refrigeration industry is increasingly using flammable refrigerants in order to achieve climate protection targets. The disadvantage of flammability is therefore no longer reserved for natural refrigerants, but also affects refrigeration machines with synthetic refrigerants.
Another argument against synthetic HFO refrigerants is the decomposition product trifluoroacetic acid (TFA). In various studies investigating the input of trifluoroacetic acid from the atmospheric decomposition of R1234yf, an increase in the TFA concentration in the environment was detected. TFA is classified as a severe water pollutant and is difficult to degrade. Although the use of R1234yf reduces the global warming potential, the overall picture is one of additional environmental impact. There is therefore a question mark over the future of HFO refrigerants.
When purchasing a temperature control unit, it is therefore quite appropriate to check the long-term investment security. In this context, the availability of synthetic refrigerants can become a problem. The recent market turbulence has shown that prices can explode overnight and, in the worst case, a refrigerant can be withdrawn from the market altogether. No one can predict whether the legal situation will tighten further in the next few years, possibly beyond the restrictions known today. It should therefore be carefully checked whether the refrigeration system may still be operated and maintained in 5, 10 or 15 years. Refrigeration systems with natural refrigerants are on the safe side in this respect.
In practice, natural refrigerants show considerable advantages over their synthetic derivatives. The refrigerant R290 has very good thermodynamic properties. Advantages include low pressure losses in pipelines and heat exchangers, the low energy requirement for compression, the smaller quantity of refrigerant required and good material compatibility. The operating behavior is even significantly better than that of R507A, R404A and the substitute refrigerant R449A. Disposal of R290 is also easier than with synthetic materials. Since propane is a natural substance, it can be released into the atmosphere in a controlled manner.
The case study of a Petite Fleur process thermostat (→ Fig. 3) on a 2-liter glass reactor shows the performance of a unit using the natural refrigerant R290. The circulator reaches a cooling capacity of 0.48 kW and covers a temperature range from -40 to +200 °C. In the case study, a cooling and heating process were documented. The case study shows that the small Petite Fleur cools the jacket from +100 °C to -20 °C within 70 minutes. The graph (→ Fig. 4) demonstrates the precision and stability of the cooling process.
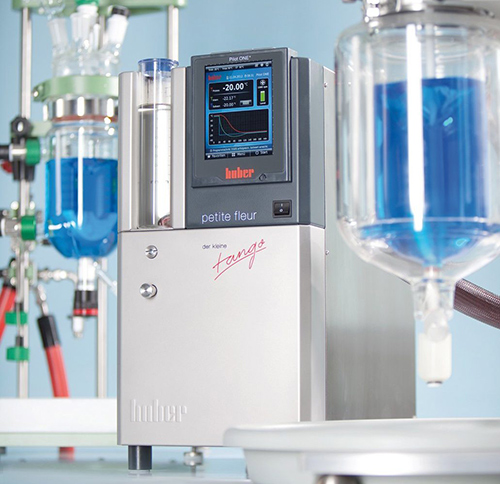
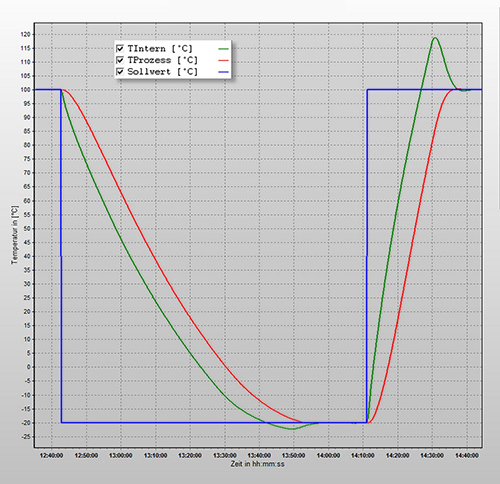
With the presentation of the Unichiller CO2 models (GL series), Huber took the next step in the development of environmentally compatible temperature control solutions. The circulators operate with CO2 (carbon dioxide, also R744) as refrigerant. The colorless gas, liquefied under pressure, has no ozone depletion potential and, with a GWP = 1, has negligible global warming potential. One disadvantage is the high operating pressures. Consequently, component prices are currently still higher than for conventional refrigeration systems. However, the market share of CO2 refrigeration systems has been growing rapidly for years, increasing component availability and decreasing prices. The thermodynamic advantages of CO2 as well as the good availability and safety speak for themselves and enable future-proof planning.
The future belongs to natural refrigerants. No matter what needs to be tempered or cooled in the laboratory - from distillation apparatus to analytical equipment to research reactors - natural refrigerants contribute to a positive environmental balance. There are no limitations in performance, and safety concerns are also unfounded when operated properly. When selecting a temperature control unit, users should keep in mind that the unit will be in use for many years. During this time, the refrigerant will have a significant impact on energy consumption. Choosing a refrigerant that is designed for sustainability eliminates the need for costly retrofits at a later date and protects against additional investments due to new regulations and laws.
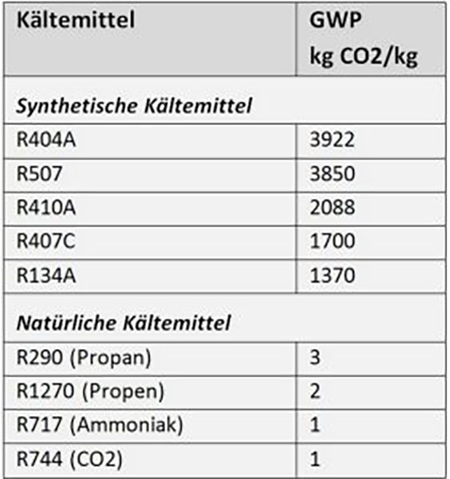
As early as the 1970s, Peter Huber developed the first chillers with natural refrigerants. In 1982, the "Environment Plus" action program was launched, which encompassed all concerns in the area of environmental protection and pushed the further development of resource-saving temperature control technology at an early stage. As early as 1993, Huber customers were able to work with CFC-free temperature control units, many years before the statutory phase-out date. Gradually, the standard models were converted to natural refrigerants. Today, almost the entire range of laboratory equipment is equipped with natural refrigerants as standard. In 2018, over 90% of all temperature control units sold were delivered with natural refrigerants. Even larger units are optionally available with natural refrigerants.