10 things that are done wrong when tempering
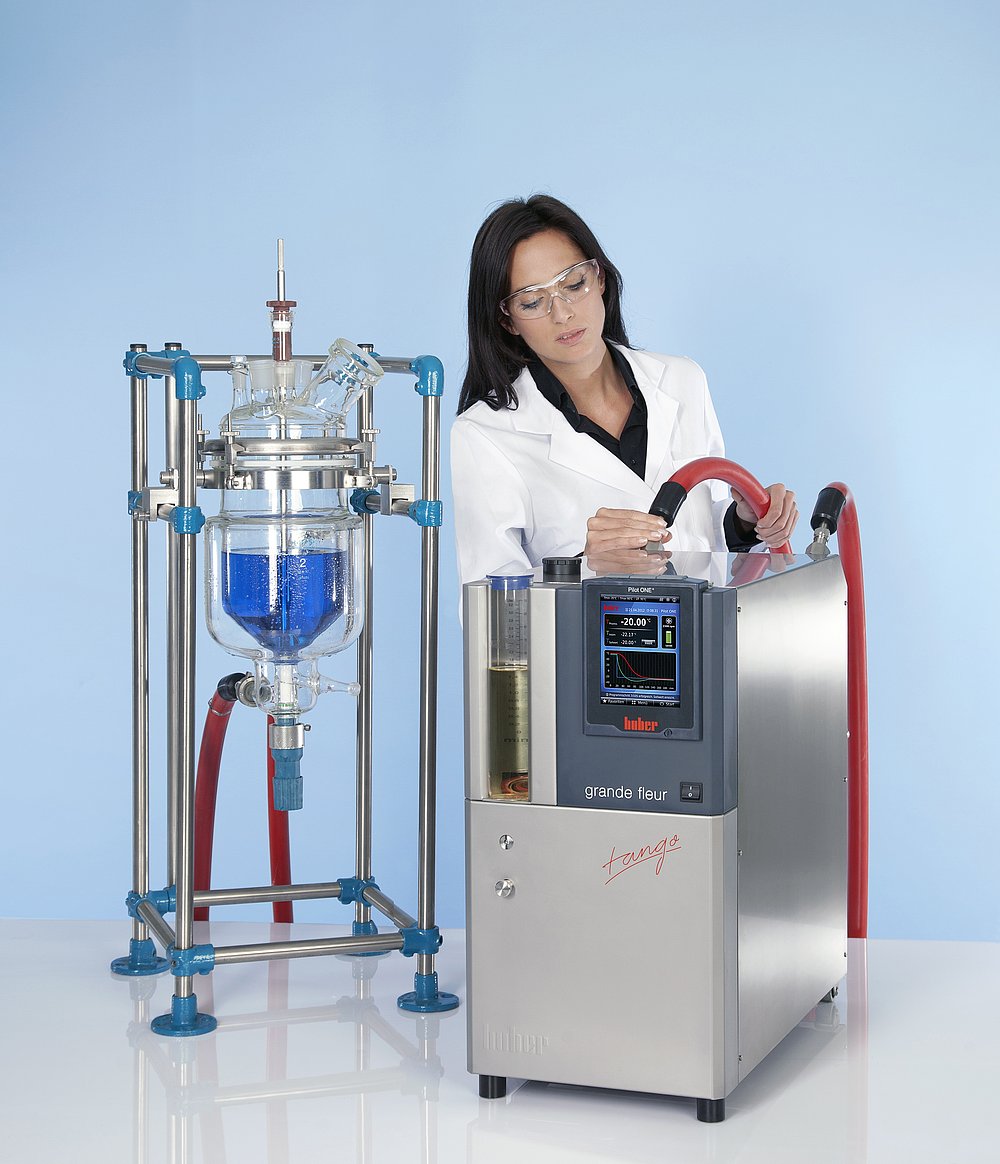
Although the temperature control unit itself has the greatest influence on the temperature control performance, the installation of the entire system should still be carefully checked. Here, too, there are numerous aspects that have a direct influence on the temperature control result. Points with a negative effect are, for example, squeezed hose connections, unnecessarily long connection paths or a small cross-section of the hoses or hose adapters. In addition, the quality and condition of the temperature control hoses also affect the achievable performance. Metal hoses with a smooth inner wall are therefore available for Unistats. These hoses improve the flow behavior and thus the heat transfer - resulting in significant time savings during heating and cooling.
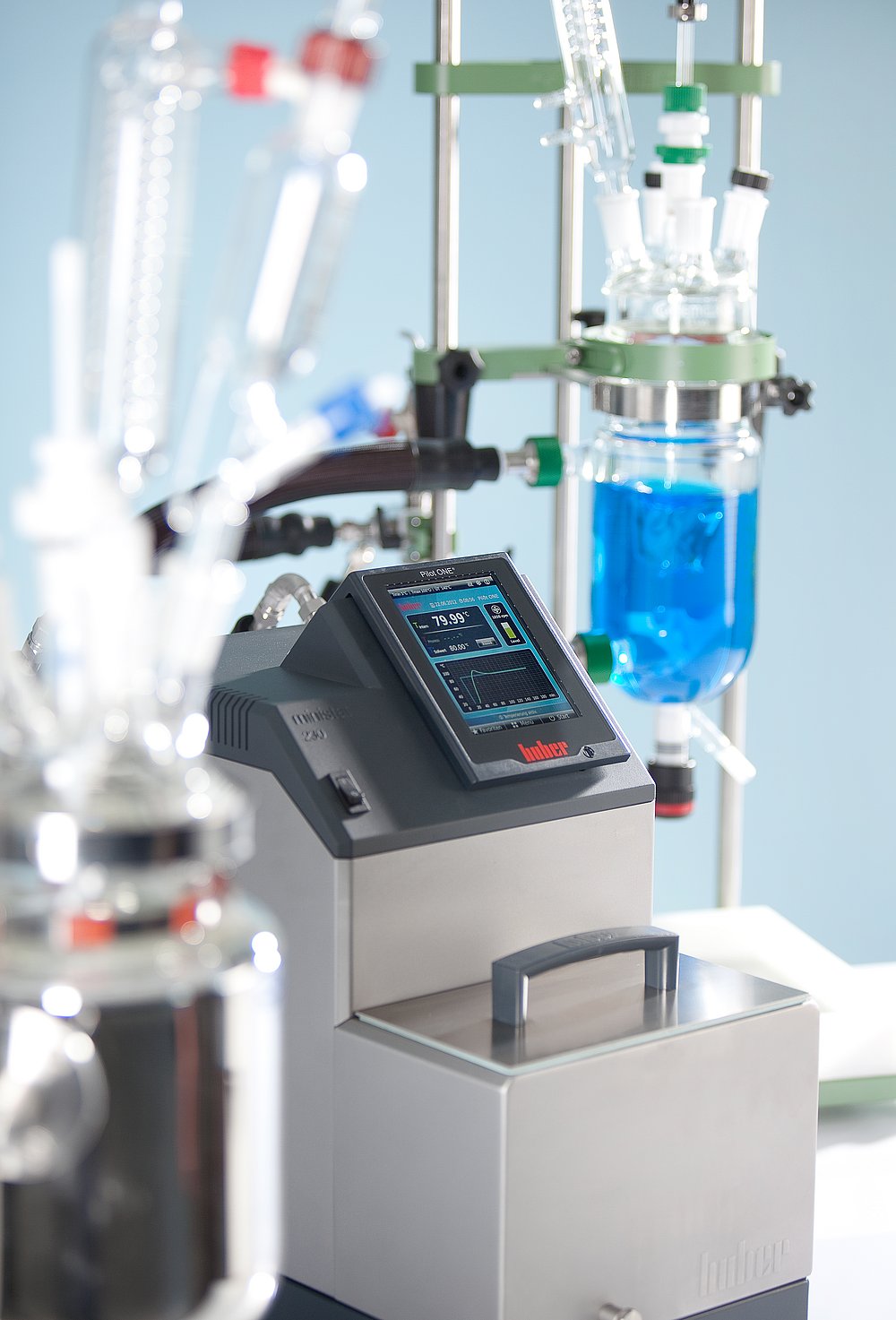
Temperature control is not about how much power a thermostat generates, but much more about the efficiency of heat transfer to the process. Generated power is useless if it is not efficiently transferred to the application. Circulators are therefore ideally designed so that turbulent flow generates a large heat transfer coefficient and thus efficient heat transfer to the internal heat exchangers (evaporator and heater). Unistat pumps therefore prefer to generate circulating flow rather than circulating pressure. The entire fluid circuit of a Unistat is also optimized for minimum internal pressure losses. This results in higher flow rates and significant optimization of heat transfer for even faster response time to control the process.
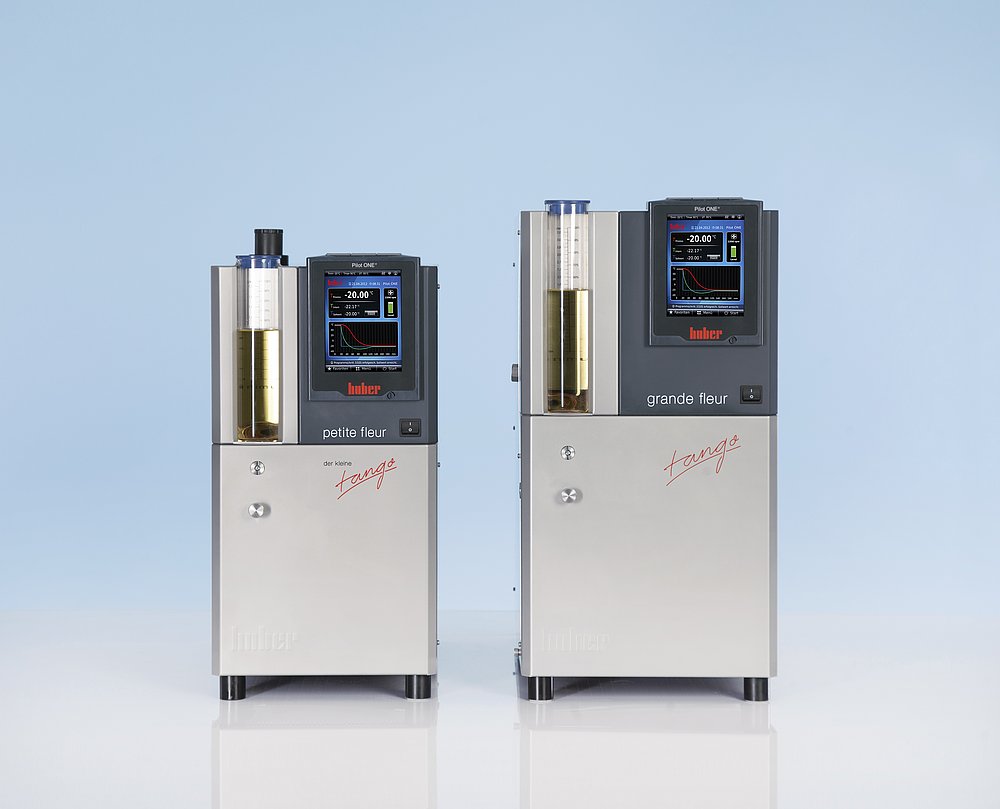
When asking about the dynamics of a temperature control unit, the heating or cooling capacity (kW) is usually used as a comparative variable. However, the power generated in the thermostat alone is not sufficient for a meaningful evaluation. An equally important aspect is the mass to be tempered. For a meaningful comparison, therefore, the cooling power density (Watt/liter) according to DIN 12876 is the most suitable. Basically, the greater the cooling power density, the more dynamically (quickly) a thermostat can respond to a change in temperature.
Here is a small calculation example: Two temperature control units from different suppliers have the same cooling and conveying capacity and are connected to identical applications. Temperature control unit 1 has a mass of 5 kg, temperature control unit 2 has a mass of 10 kg. The mass of the external application is 5 kg. In the first case, the total mass is 10 kg (internal filling volume plus external application), in the second case, 15 kg must be cooled or heated. The ratio is 2 : 3, or in other words: it takes only 2/3 of the time with temperature control unit 1. The time saving is therefore 33%.
This example shows that the cooling capacity is certainly an important factor. However, this should then be related to the quantity of temperature control liquid used. The result is the cooling capacity density, which allows a meaningful comparison (see DIN).
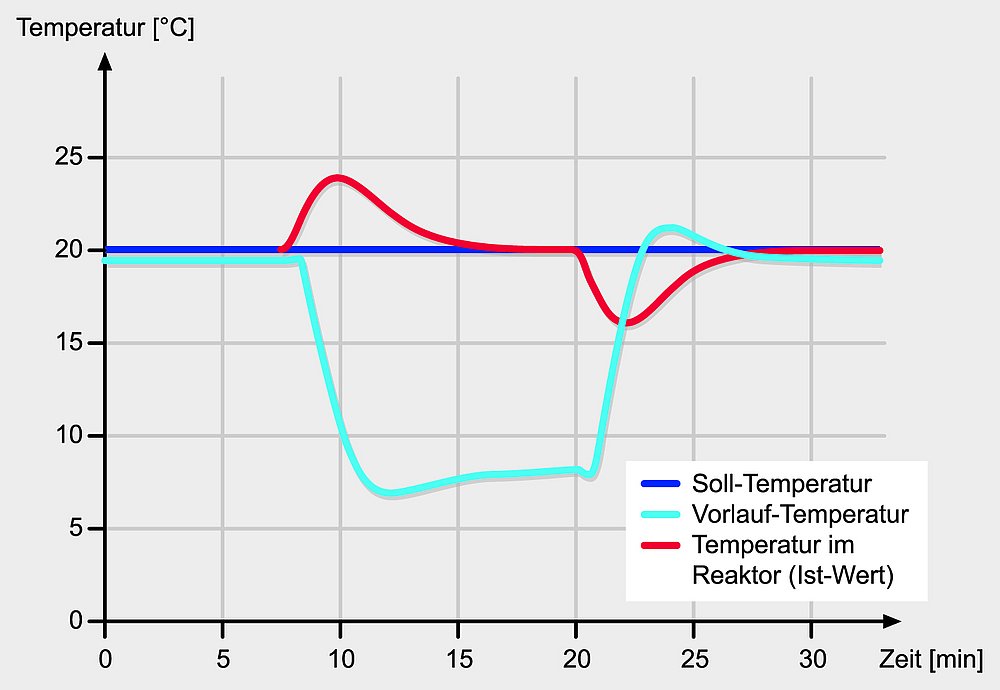
If the control electronics of the temperature control unit are not matched to the application, the best controller is of no use. The consequences of incorrect control parameters are slow heating and cooling, inaccurate control, and overshooting or undershooting when regulating. By using intelligent, self-optimizing control such as Huber's TAC (True Adaptive Control), such problems can be circumvented. Compared to most automatic PID controllers, True Adaptive Control goes one step further. TAC analyzes the controlled system over the entire temperature range and generates a multi-dimensional model. As a result, the temperature controller is always supplied with the best control parameters and adapts optimally even when plant conditions fluctuate greatly. This means that quality specifications for the temperature controller can be optimally adhered to and the controller always achieves the shortest possible control times.
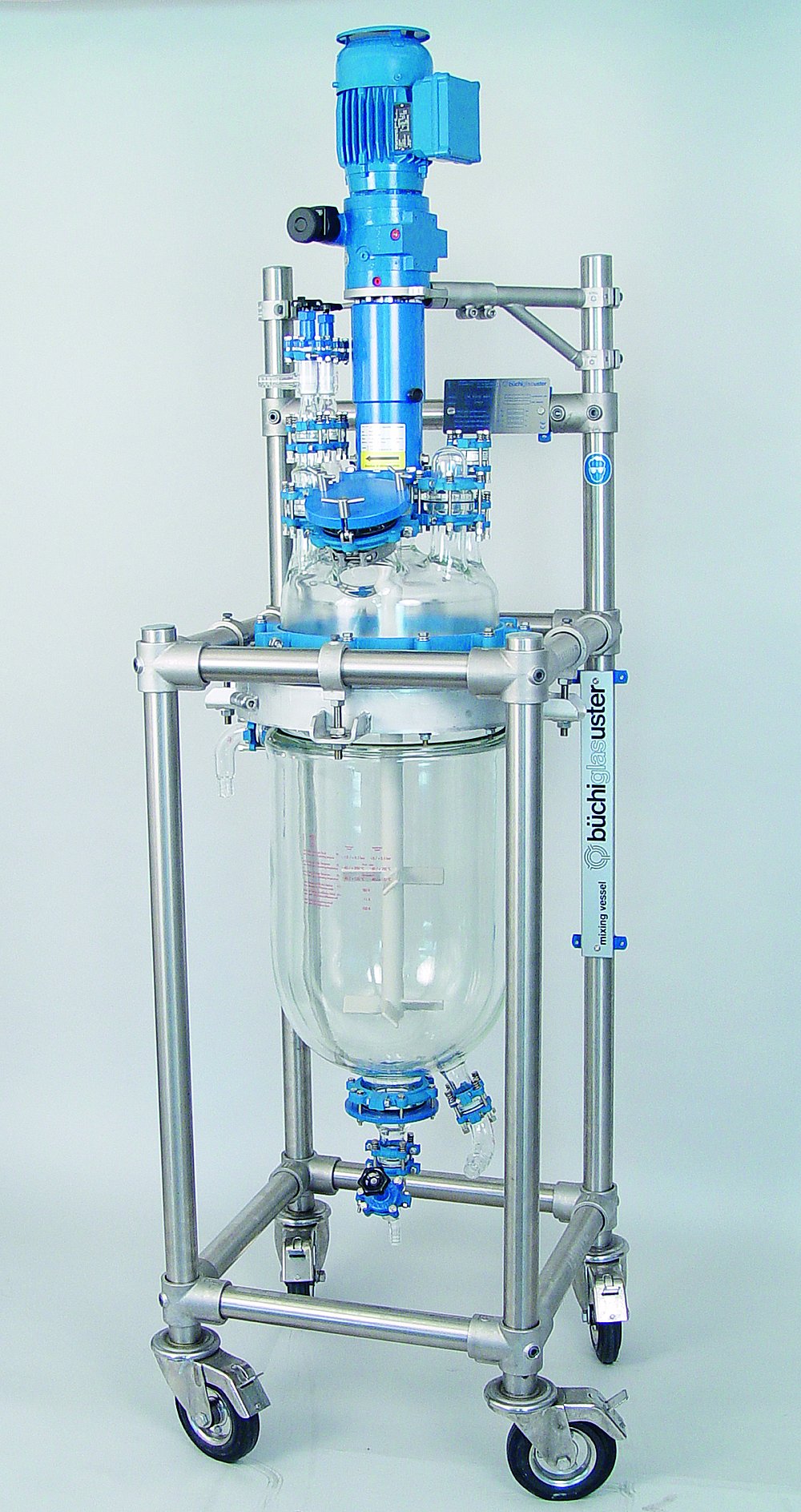
Many temperature control units on the market have a high pump pressure in the standard configuration - often too high for sensitive glass reactors! With these devices there is a risk of bursting. Unistats for laboratory use are therefore equipped with a speed-controlled pump with soft start. The pump pressure is controlled by a pressure sensor. Large unistats with high performance control the pressure via an infinitely variable bypass and thus ensure maximum flow within the set pressure limits. Care should also be taken in this context when using quick-action couplings. Once a test is complete, either the flow or the return into the reactor must remain open. Otherwise, there is a risk of the reactor bursting because the "enclosed" temperature control liquid heats up and expands (overpressure).
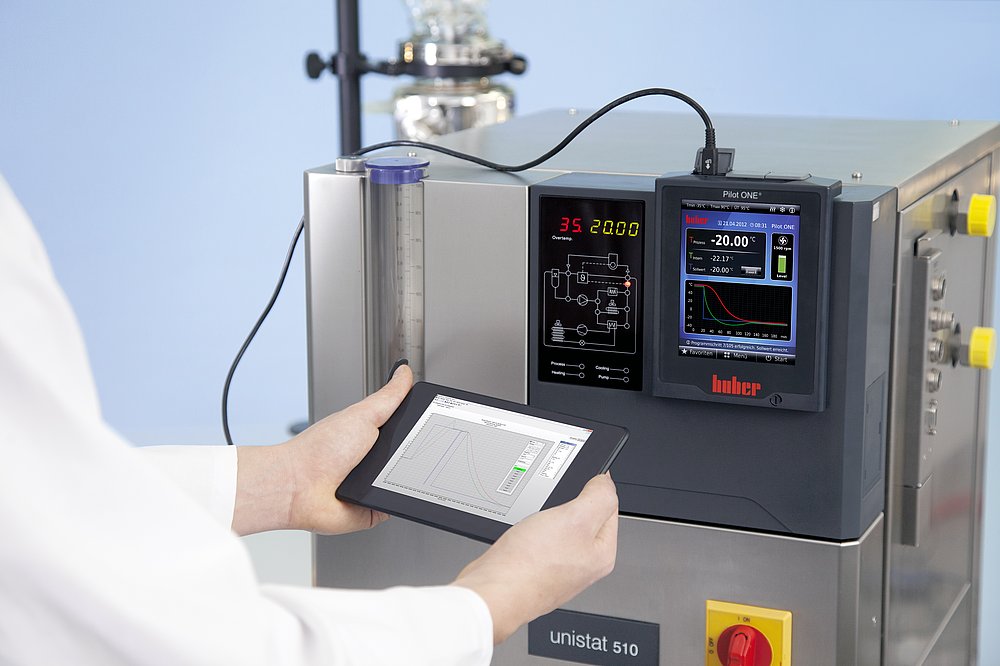
Many applications require frequent temperature changes. If the setpoint has to be constantly readjusted by hand, this is cumbersome, time-consuming and error-prone. In such cases, an integrated programmer ensures significantly more efficient operation. With the integrated programmer in Unistats, individual temperature steps or extensive temperature sequences with up to 100 program steps can be realized. In addition, a non-linear ramp function is available especially for crystal growing, resulting in higher degrees of purity. Instead of complex step profiles, any e-functions can be defined as continuous setpoints. Another advantage: the created temperature control profiles can not only be permanently stored in the unit, but can also be easily saved via USB stick and copied to another unit (works for all units with Pilot ONE controller).
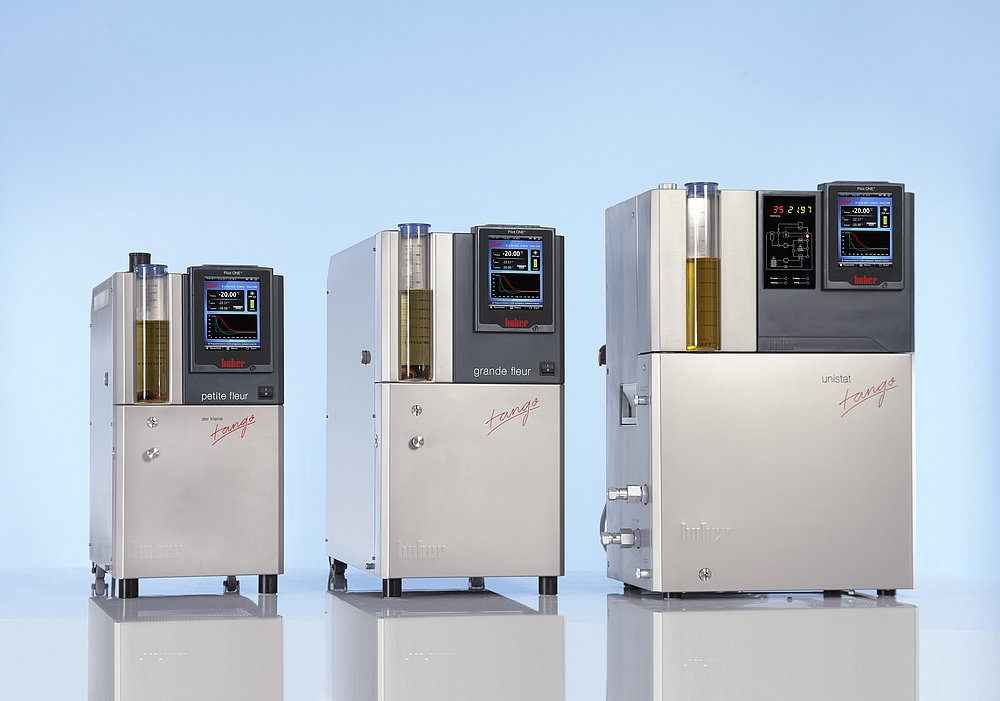
If a chemical process is scaled up from laboratory scale to production, consistent technology is advantageous. Problems arise at the latest when the laboratory temperature control unit is not available in a larger model variant for production. This is because a system change inevitably brings with it a change in temperature control behavior and thus makes a reliable scale-up calculation more difficult. A constant temperature control solution is therefore preferable. The Unistat range therefore includes over 60 standard models with cooling capacities from 0.7 to 130 kW. Unistats are thus ideally suited for flexible scale-up in research, kilo lab, miniplant, pilot plant and production. Smallest quantities are tempered just as much as production quantities and this at working temperatures from -125 °C to +425 °C.
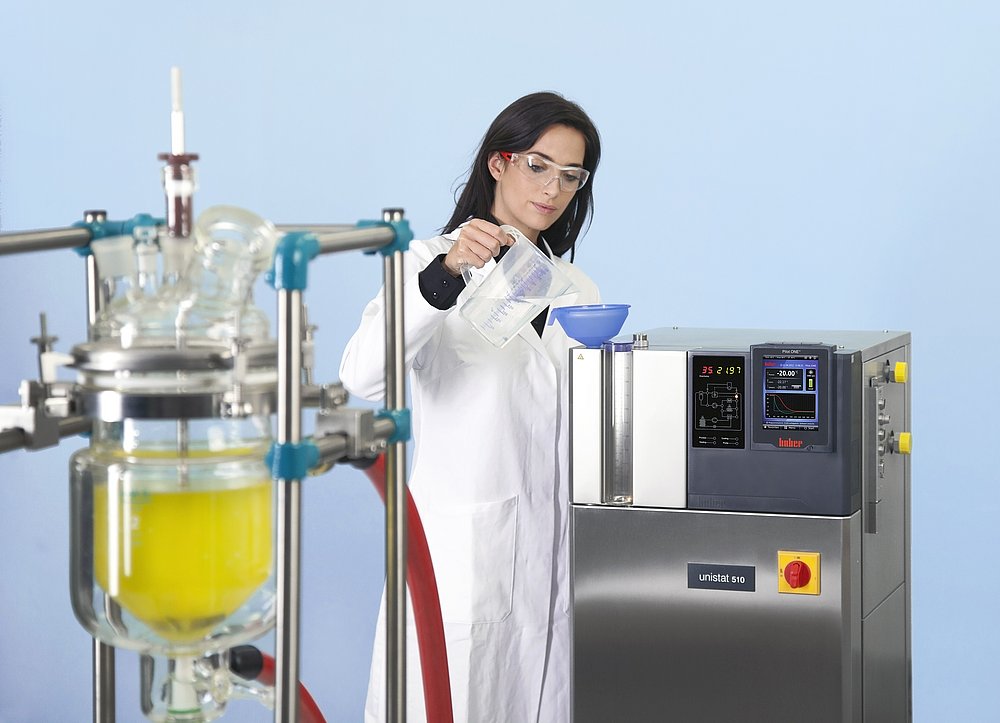
In temperature control units with a closed liquid circuit, outgassing of the temperature control liquid is very important. This involves the targeted removal of foreign substances and impurities, such as those that can arise from residues in hoses or in the reactor. For this purpose, the temperature control liquid is heated until the impurities escape as gas bubbles. If outgassing is not carried out correctly, uncontrolled conditions can result later during operation. Unistats offer a convenient automatic mode both for degassing and for venting the system.
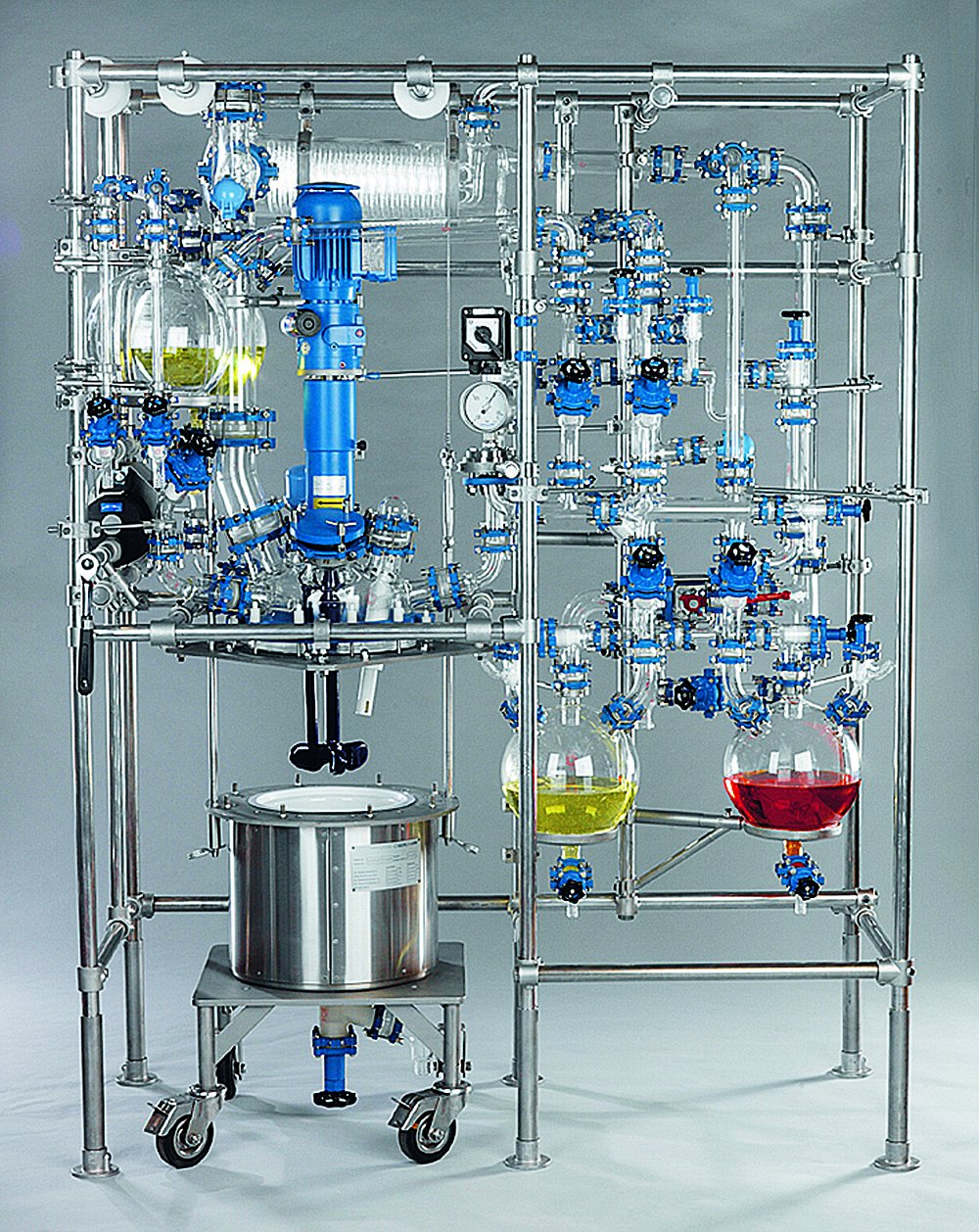
As a rule, modern temperature control units have protective devices for overtemperature and low level. Most standard situations therefore do not cause any problems. The situation is different for complex error scenarios, which do occur in practice. A typical example is a safety shutdown due to an overtemperature caused by an exothermic reaction. In most temperature control units, circulation and cooling are completely switched off, i.e. the reaction energy drives the temperature in the reactor up unchecked, if necessary. This can result in the destruction of expensive materials to be tempered! With Unistats, additional protective functions ensure that the circulating pump and refrigerating machine continue to operate despite overtemperature shutdown. This enables controlled heat dissipation in the event of a malfunction or in the event of unforeseen reaction sequences and protects the temperature-controlled product from damage.
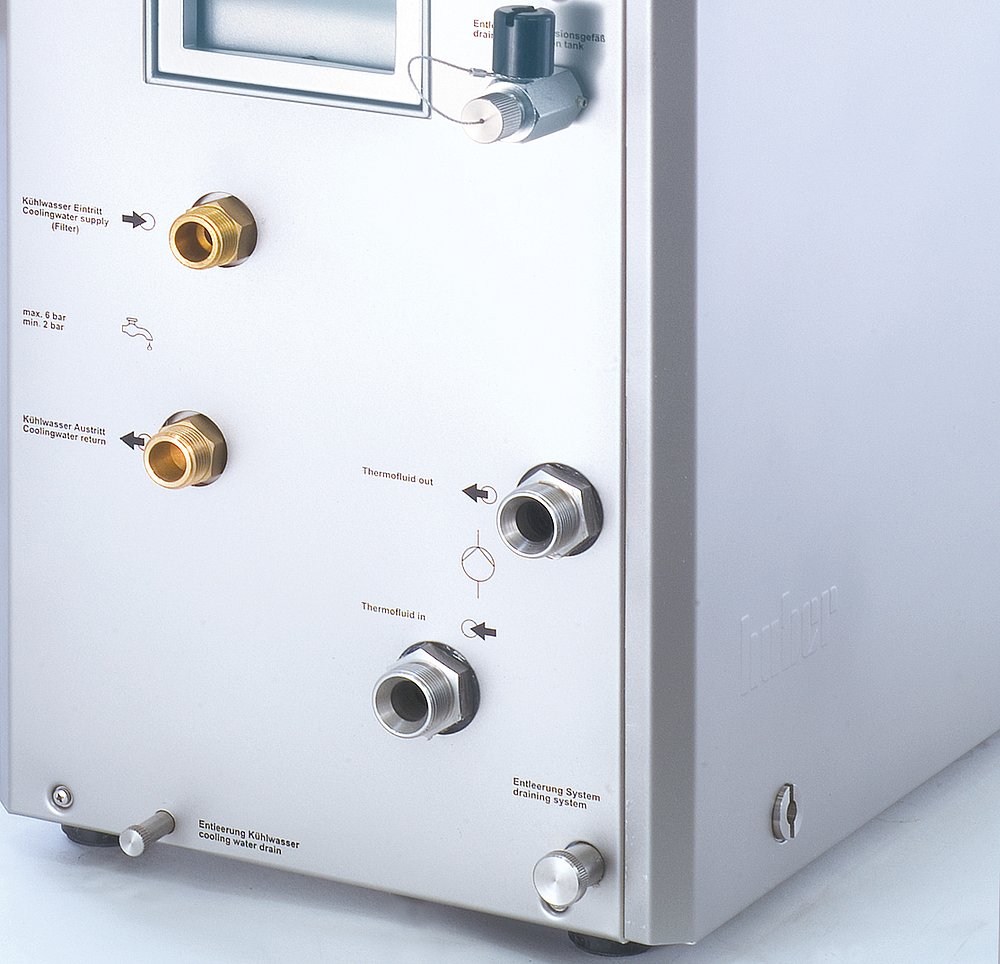
Applications with a closed temperature control circuit are still sometimes operated with conventional bath thermostats for supposed cost reasons. However, closed-loop temperature control systems, also known as process thermostats, are a powerful alternative. The device class of process thermostats was first launched over 25 years ago with the "Unistat Tango". The then completely new concept of the Unistat Tango brought a major technological advance in temperature control. In contrast to conventional bath and circulation circulators, Unistats operate with a closed temperature control circuit. This principle reduces the masses to be tempered and thus increases the rates of temperature change. The Unistat technology offers further advantages: in the hydraulically sealed temperature control circuit, there is hardly any oxidation of the temperature control fluid. The service life of the thermofluid is thus noticeably longer. The thermofluid can also be used in a wider operating temperature range. The low internal filling volume means that less thermofluid is required overall. Unistats therefore save money threefold and reduce operating costs! The somewhat higher investment in a Unistat (compared to a conventional bath circulator) therefore pays for itself after a short time.
When it comes to process temperature control, there are a number of points to consider in order to achieve an optimum result. Modern process thermostats such as the Unistats relieve the user of many tasks. For this purpose, the devices are equipped with intelligent automatic functions and feature a proven safety concept. The result is the best possible process reliability as well as reliable and reproducible temperature control behavior. With their versatile connection options via RS232, RS485, USB, Ethernet, Profibus, etc. and support for Industry 4.0 standards such as OPC-UA, Unistats are also ideally suited for integration into an automated production environment.